How to find the correct paint system
How can one choose and describe a procedure for painting a subject in a given construction material when specific influences are foreseen at the subject's place of use?
You start with a functional analysis.
The functional analysis mainly applies to the cover painting, as the procedure establishes a number of requirements you want to be fulfilled. For example, the following:
- Gloss and colour fastness
- Weather resistance
- Chemical resistance - acids and bases
- Heat resistance
- Repair friendly
- Cleanable
Given this, we can inform you which cover paint best meets the requirements.
You can then decide how the treatment should be built up.
Selection of corrosion classes
For the treatment of steel structures with corrosion-protected paint systems, a selection procedure has been developed based on the definition of corrosion classes cf. DS/EN ISO 12944.
Corrosion class no. |
The aggressiveness of the environment |
Environmental examples |
C1 |
Very low |
Indoors in dry rooms. (Relative humidity < 60%) |
C2 |
Low |
Indoors in unheated well-ventilated rooms. eg. depots and sports halls. |
C3 |
Middle |
Indoors with changing humidity. In a country atmosphere, far from industry and densely built-up areas. |
C4 |
High |
In densely built-up areas, industrial areas over water and on coasts. |
C5 |
Very high |
Industrial areas with high humidity and aggressive atmosphere. Coastal areas with high salt concentration. Indoors in buildings with constant condensation and high pollution. |
CX |
Extreme |
Offshore. |
Paint systems - Steel structures
The following treatments can be used, depending on the corrosion class:
Corrosion class C1:
Pretreatment: |
Steel brushing or cleaning in thinner |
|
One-coat: |
EFAcombi AK 164 |
60µm |
|
Total layer thickness |
60 µm |
Corrosion class C1 - water-dilutable alternative:
Pretreatment: |
Steel brushing or cleaning in EFAdeck Cleaner |
|
One-coat: |
EFAcombi AK 560 |
60µm |
|
Total layer thickness |
60µm |
Corrosion class C2:
Pretreatment: |
Degreasing and then cleaning to min. St 2 according to ISO 8503 St 3. |
|
Priming: |
EFAguard AK 103 |
40 µm |
Cover Paint: |
EFAtop AK 167 |
40 µm |
|
Total layer thickness |
80 µm |
Corrosion class C2 - water-dilutable alternative:
Pretreatment: |
The surface must be clean and free of contamination before painting, according to ISO 12944-4. They were cleaned to min. St 2 according to ISO 8501-1. |
|
Priming: |
EFAguard AK 564 |
50 µm |
Cover paint: |
EFAcombi AK 560 |
50 µm |
|
Total layer thickness |
100 µm |
Corrosion class C3:
Pretreatment: |
The surface must be clean and free of contamination before painting, according to ISO 12944-4. Sandblasting to Sa 2½ according to ISO 8501-1 |
|
Onecoat: |
EFAcombi PU 434 |
120 µm |
|
Total layer thickness |
120 µm |
Corrosion class C3 - water-dilutable alternative:
Pretreatment: |
The surface must be clean and free of contamination before painting, according to ISO 12944-4. Sandblasting to Sa 2½ according to ISO 8501-1 |
|
Priming: |
EFAguard 564 |
80 µm |
Cover paint: |
EFAcombi AK 560 |
80 µm |
|
Total layer thickness |
160 µm |
Corrosion class C4 - medium - polyurethane system:
Pretreatment: |
The surface must be clean and free of contamination before painting, according to ISO 12944-4. Sandblasting to Sa 2½ according to ISO 8501-1 |
|
Priming: |
EFAcombi 433 |
90 µm |
Cover paint: |
EFAcombi 433/434/435 |
90 µm |
|
Total layer thickness |
180 µm |
Corrosion class C5 and CX:
We currently do not produce products for these corrosion classes
If you have any questions, you can contact our experts here, or directly to our sales manager for industry Anders on tel: +45 28 10 60 52
Aluminium and hot-dip galvanized surfaces.
In general:
Pretreatment of hot-dip galvanized surface.
Surface treatment of hot-dip galvanized (galvanized) surfaces requires special pretreatment. Therefore, we recommend the following procedure:
Mix 3-fold alcohol (ammonia) and water in a ratio of 1:4. Pour one dl of washing-up liquid into a mixture of 5 litres. The galvanized surface is scrubbed with a nylon sponge (e.g. Scotch Brite) until the resulting foam turns grey. The surface is rinsed with clean water and is ready for priming after drying.
Pretreatment of aluminium
Aluminium can be degreased with Esbjerg Grundrens and mixed with water in a ratio of 1:10. Remember to rinse with clean water, as soap residue on the surface will otherwise destroy the adhesion.
Corrosion class C1 + C2:
Priming: |
EFAmetal Shopprimer, series 0200 |
15 µm |
Cover paint: |
EFAmetal Maskinemalje, series 0130 |
35 µm |
|
Total layer thickness |
50 µm |
Korrosionsklasse C1 + C2 - vandfortyndbart alternativ:
Priming: |
EFAmetal H2O Shopprimer, series 0561 |
25 µm |
Cover paint: |
EFAmetal H2O Enamel, series 0551 |
30 µm |
|
Total layer thickness |
55 µm |
Corrosion class C3:
Priming: |
EFAmeal PUR priming, series 0446 |
35 µm |
Cover paint: |
EFA One Coat Finish, series 0164 or EFAmetal Machine Enamel, series 0130 |
30 µm |
|
EFA One Coat Finish, series 0164 or EFAmetal Machine Enamel, series 0130 |
30 µm |
|
Total layer thickness |
95 µm |
Corrosion class C3 - water-dilutable alternative:
Priming: |
EFAmetal H2O Shopprimer, series 0561 |
30 µm |
|
EFAmetal H2O Shopprimer, series 0561 |
30 µm |
Cover paint: |
EFAmetal H2O Enamel, series 0551 |
35 µm |
|
Total layer thickness |
95 µm |
Corrosion class C4:
Priming: |
EFAmetal PUR Primer, series 0446 |
30 µm |
|
EFAmetal PUR Primer, series 0446 |
30 µm |
Cover paint: |
EFAmetal PUR Enamel, series 0440 |
35 µm |
|
EFAmetal PUR Enamel, series 0440 |
35 µm |
|
Total layer thickness |
130 µm |
What is ISO 12944?
ISO 12944 is an international standard for determining corrosion classes. It is a document that describes the different types of corrosion classes and their properties. This is used for steel structures to determine which paint system is the right one for a given job. It is categorized by the classes c1, c2, c3, c4, c5 and cx, which are på paint systems for offshore.
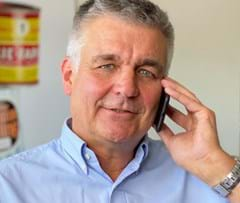